The Seed Train in Bioprocessing Design, A Journey from Micro to Macro
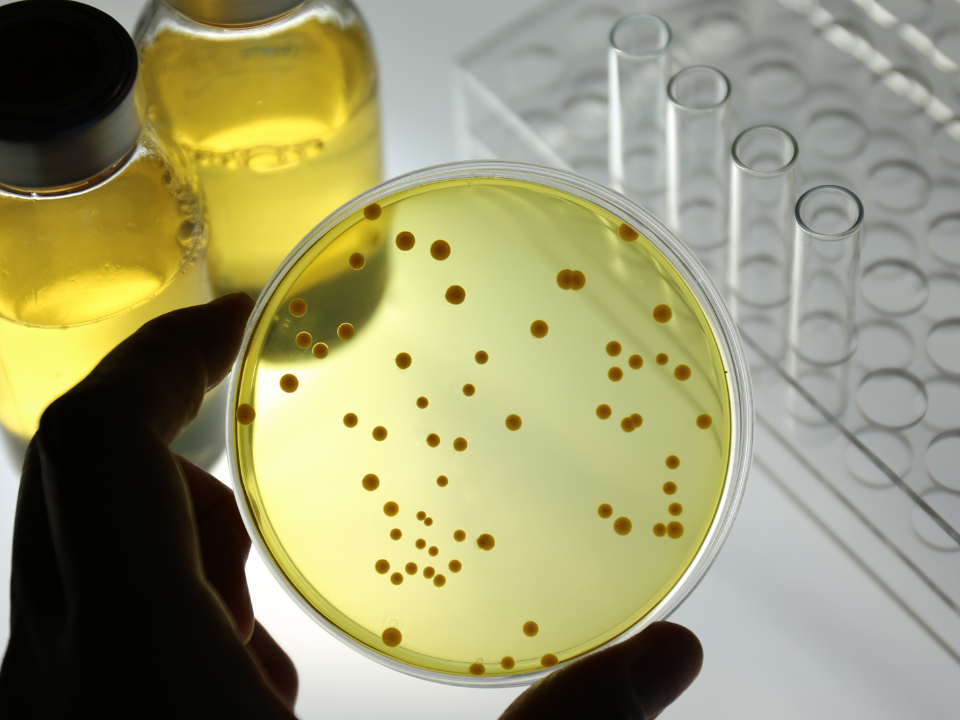
In the world of bioprocessing, the journey from a petri dish culture to a bioreactor full of microorganisms would be characterized by the process of seed train. These represent essential chapters in the story of bioprocess production. Understanding what is behind bioprocess design and development is essential to achieving the highest productivity and efficiency in this complex field.
What is "Seed Train" in Bioprocessing?
A seed train refers to the initial culture of microorganisms or cells that are used to start a larger-scale production process. This culture is carefully selected, characterized, and grown under controlled conditions to create a consistent and viable starting material for the subsequent steps in the production process. To get that an accurately planned series of cultures increases the biomass of microorganism production. Generally, before the initiation of the main culture on a larger scale, three to five precultures are prepared including seed train, inoculum train, and production run. The preparation is in a stepwise process, at each step, both the volume and cell density are increased from the previous step, a process known as "scaling up". The number of cultures and steps involved in its multiplication can vary in relative need and the type of microorganism or cell line being used.
'Seed Train: Culturing from initial cells to the main bioreactor.'
Tailoring the Seed Train for Different Microorganisms
The preparation of the seed train differs significantly depending on the type of microorganism or cell line to be grown. Each of these may have very specific definitions for growth parameters, metabolic needs, and environmental sensitivities. For example, E. coli grows very fast, usually having only a few stages and relatively simple media.
While mammalian cells, such as CHO cells, grow at lower rates compared to microbial cells and require complex, serum-supplemented media. They are more sensitive to shear forces. Some fungal cultures can show very complex morphologies, for the most part, they have also led to the design of special agitation rates. These differences show the need for a seed train process that can be tailored to assure efficient, scalable, and consistent production applicable to the organism's requirements.
The Impact of the Seed Train on Bioprocess Design
As with any good story, the details matter. The design and optimization of the seed train and preculture stages can influence the entire bioprocessing. Here are three concepts the seed train can impact at the early-stage preparation of the bioprocess: maintaining, scalability, and consistency.
- Maintaining:
The cells are our characters in the story, therefore, their health and vitality must be maintained. If the cells are not growing properly, it will be the reason for a suboptimal growth and productivity rate. Preparing multiple cultures ensures that the cells reach a high density and are in an active growth phase (typically the exponential phase) before being transferred to the next stage. This maximizes the inoculum’s potential for robust growth in the subsequent culture, leading to a more efficient production process.
- Scalability:
The scalability of the seed train is like the development of a small start-up into a multinational company. It must create a balanced growth environment at each step to prepare cells for further volume increases. This gradual approach is necessary to maintain cell health, viability, and productivity. A sudden jump to a large culture volume can stress the cells, leading to suboptimal growth or even culture failure.
- Consistency:
As with any successful franchise, the experience should be very similar at each location; in bioprocessing, consistency is key. The seed train and preculture processes must be reproducibly operated so that each successive batch of cells arrives at the production stage with uniform characteristics. This requires that the same protocols and standardized quality control should be applied.
The Finale
The seed train is an essential step to successful bioprocessing. Their design has a direct impact on the efficiency, scalability, and consistency of the downstream biomanufacturing process. The suitable optimization at those first stages empowers bioprocess engineers with the capability to improve productivity, reduce costs, and ensure the robust performance of the production bioreactor.