
Data Spotlight
Enhancing S. cerevisiae Cell Growth on Potato Waste: Leveraging the Liquid Injection System (LIS) for Fed-Batch in Shake Flasks to Mitigate Growth Inhibitors
Background
The hydrolysate of potato waste contains valuable sugars that the yeast S. cerevisiae can use for cell growth and protein production. It is one preferred choice as substrate for biomass production because potatoes are the mostly consumed vegetables in developed countries. However, it also contains several growth inhibitors, like furfural, acetic acids, formic acids, and others. When accumulated, these inhibitors have a detrimental effect on cell growth and biomass production suffers. Batch cultures therefore need a careful consideration of potato waste treatment and the supplementation of this hydrolysate to the medium – too much will contract cell growth because of growth inhibitors but too less limits cell growth as well, because less sugar will be available.
Victor Pozzobon and his coworkers from Centrale Supélec, Chaire de Biotechnologie deconstructed potato waste by acid hydrolysis, making the incorporated sugars available to cells. They then tested two different operation modes - a batch and a fed-batch procedure in shake flasks to provide data on the feasibility of single-cell protein production with S. cerevisiae on potato waste and model the presumed productivity of such a process in a large-scale bioreactor.
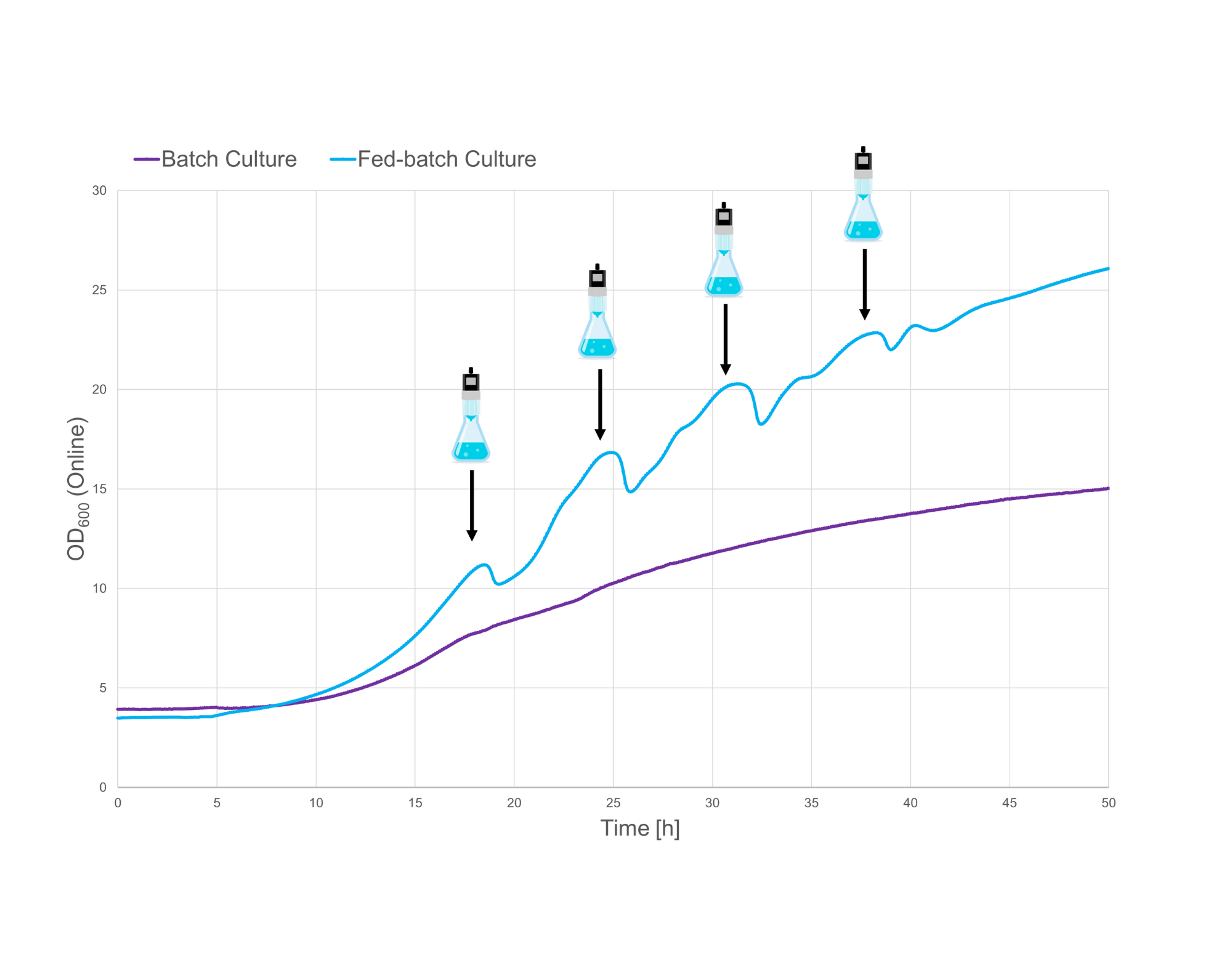
Growth profiles of S. cerevisiae cultures grown under batch (purple) or fed-batch (blue) conditions in shake flasks, in which potato hydrolysate was used as a substrate. Time points of substrate additions in the fed-batch culture are indicated by icons and were realized with the Liquid Injection System (LIS).
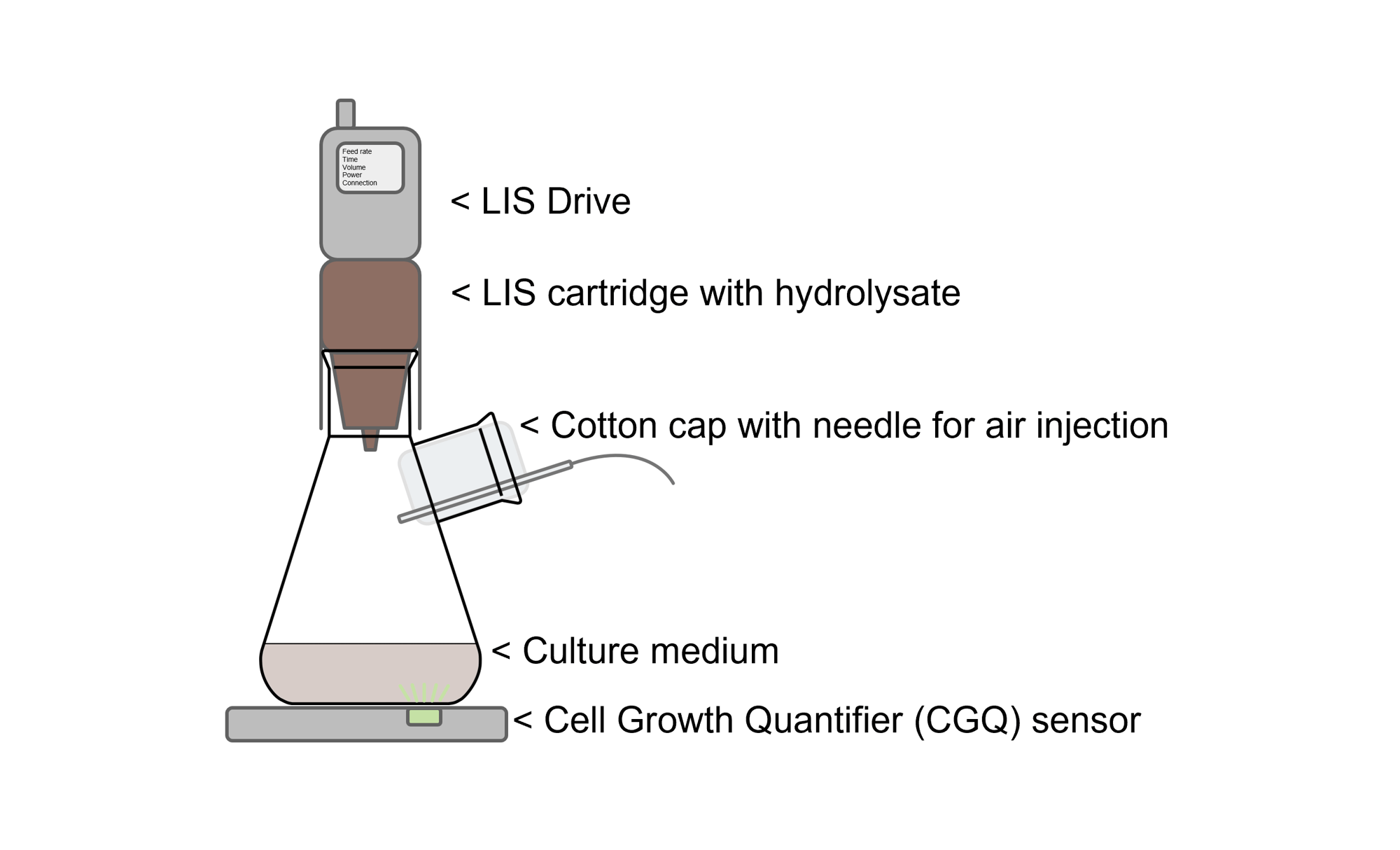
Materials & Methods
In the batch process, the substrate was completely supplied to the culture from the beginning. For the fed-batch process, the Liquid Injection System (LIS) was implemented. The scientists used a shake flask with two necks (38 mm). The second (lateral) neck was used to insert a needle through a cotton cap for air injection to avoid oxygen limitation. The LIS setup was mounted onto the primary, straight neck. The prepared concentrated hydrolysate (20 mL) was provided in the sterile LIS cartridge which was connected with the LIS Drive. A multi shot feeding profile was choosen in which 20 mL of hydrolysate were fed in 4 steps equally (5 mL each) over a cultivation time of 50 hours. Cell growth was monitored online and continuously with the Cell Growth Quantifier (CGQ) and online OD600 values were derived from a two-point calibration.
Conclusion
In the batch culture, the complete, concentrated hydrolysate was supplied to the culture from the very beginning, adding higher sugar concentrations to the medium. Also, higher amounts of unwanted substances that negatively influence yeast cell growth were present.
The fed-batch process, realized with sbi’s LIS setup, reduced the initial concentration of growth inhibitors in the medium. This concentration slowly increased with each feeding step, so that the higher cell densities that were reached in between feeding steps could tolerate the overall composition more easily. The cells could therefore utilize the sugars of the hydrolysate in the same, biomass supporting way, whereas the effect of the growth inhibitors was reduced compared to the batch procedure.
A fed-batch process improves the growth of yeast cells on concentrated potato feed because toxic effects of this substrate can be contained. With the LIS, it was possible to show this on a shake flask level, imitating bioreactor-scale runs. This allows for the collection of valuable data enabling the modeling of industrial bioprocesses, such as the production of single-cell protein from potato waste.
Source
Cui, N. & Pozzobon, V., 2022. Food-Grade Cultivation of Saccharomyces cerevisiae from Potato Waste. AgriEngineering, https://doi.org/10.3390/agriengineering4040061
Read the whole Success Story here!
Want Results Like These?
We will work with you on a solution that works best for your application.
From Estimation To High-Resolution Growth Curves
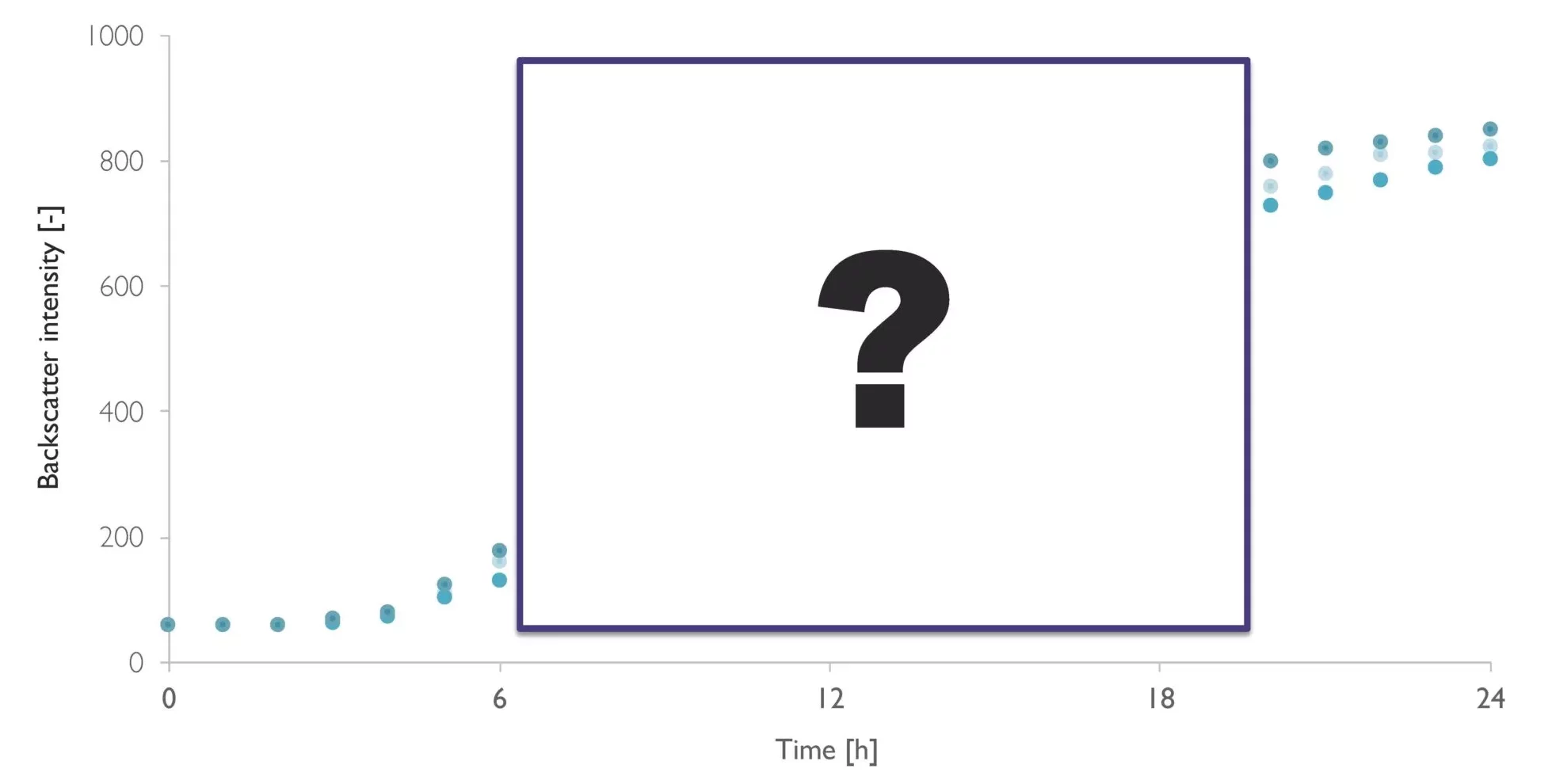
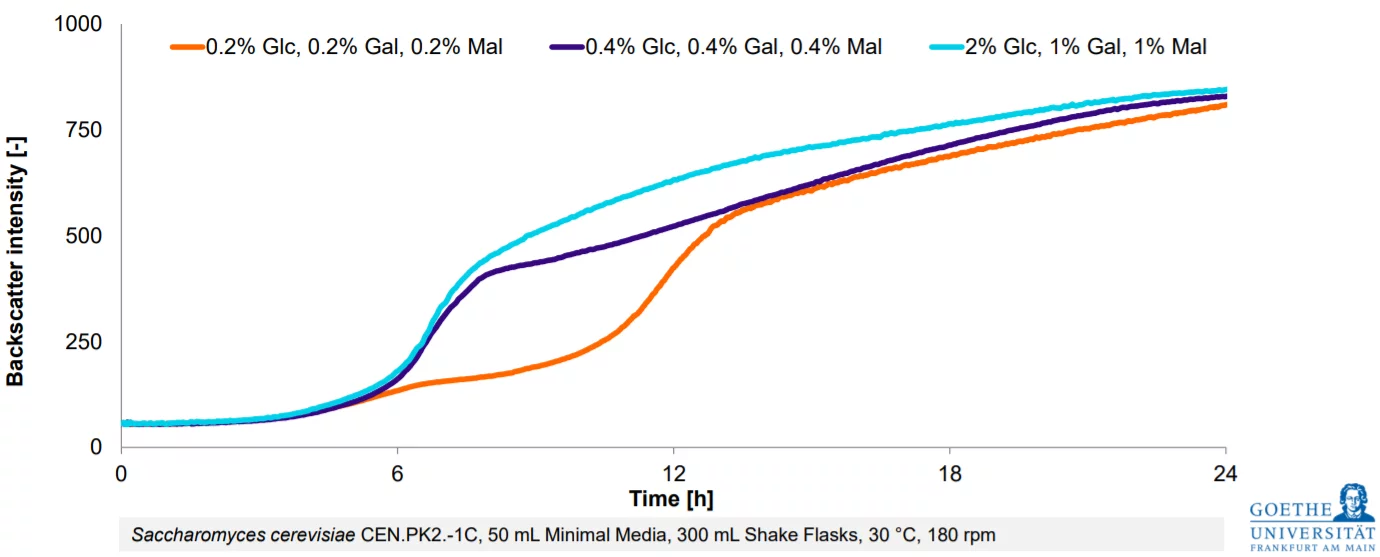
Customer Success Stories
.png)
-Kitana Manivone Kaiphanliam (Washington State University)
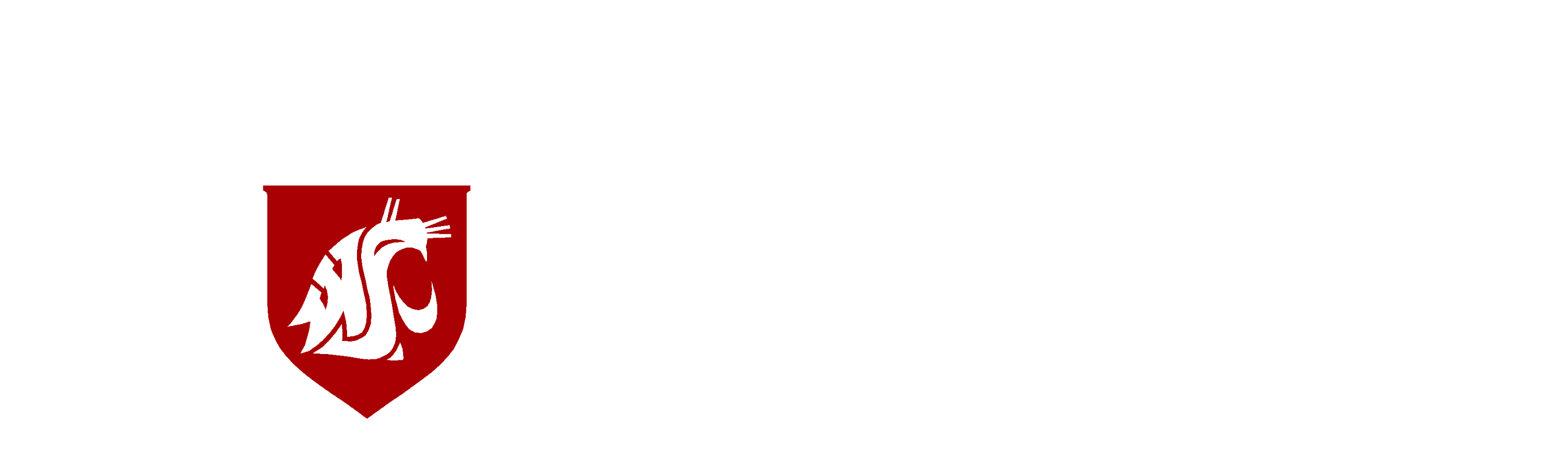